Safety Systems
Smoke Detection System
All of the MRC cleanroom facilities are protected by a fast response smoke detection system (AnaLASER System manufactured by Fenwal). This system continuously draws air through a piping network to the detection chamber. The piping network is located behind air returns and at the ceiling level, where there are no returns available. This system will detect highly diluted smoke & overheat by-products. AnaLASER has been proven to detect the plasticizers commonly released from wiring in the early phases of heat buildup, so even small scale soldering may not be performed in the cleanroom. Because of the level of sensitivity, it is critical that tools (especially those in chases) be monitored frequently and problems be taken care of immediately. The NNF Laboratory Manager and/or the Director of the NNF Facility need to approve projects that involve any soldering/welding executed in the clean room. This requires de-activation of the fire alarm system which affects the operation of the facility as a whole.
Activation of the fire alarm system (horns and strobes) requires immediate evacuation of the building.
Fire Suppression System
This system discharges CO2 in a chemical hood when it is triggered by the flash (flame) detector. All chemical hoods in NNF are equipped with this system.
CO2 pressure in the tanks can be checked using the gauges installed on the CO2 tanks.
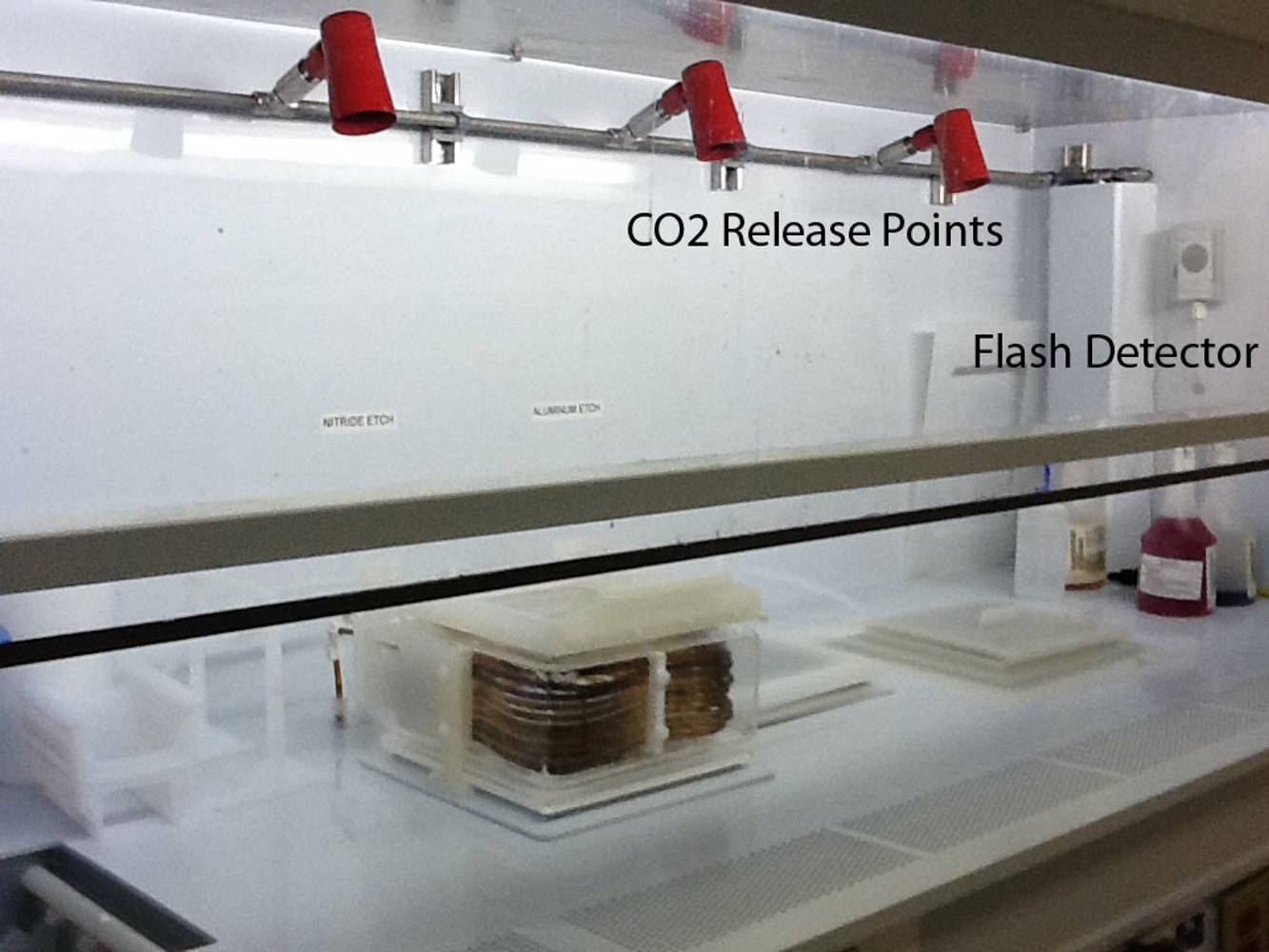
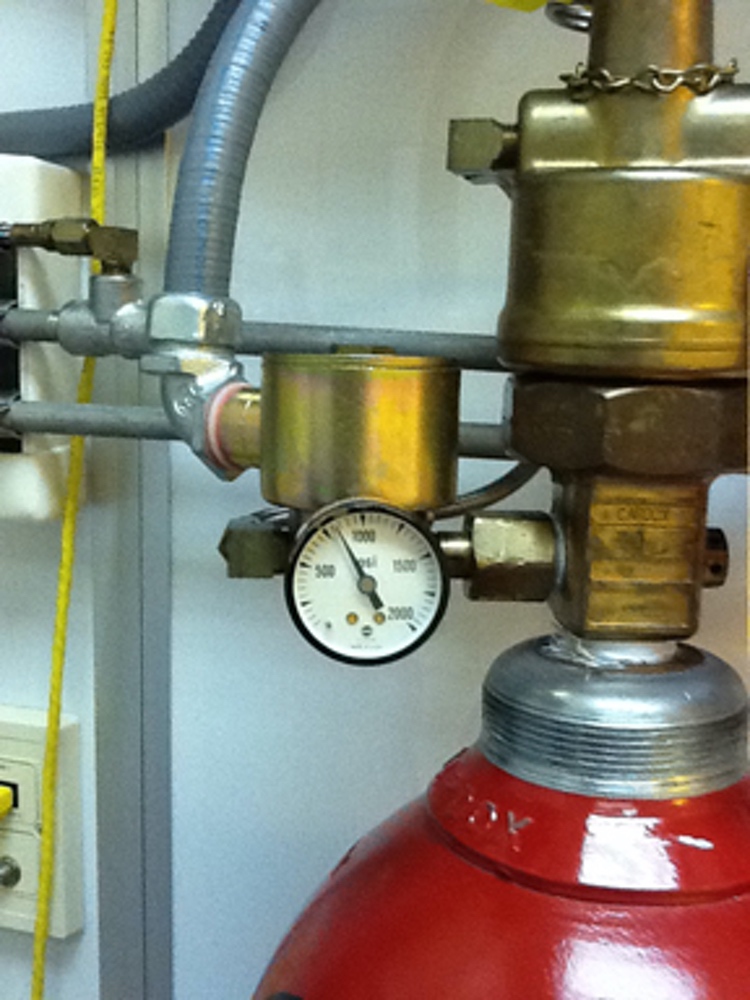
Honeywell Gas Monitoring System
The toxic and pyrophoric gas monitoring system in the MRC cleanrooms is a Honeywell system, which is a continuous monitoring system. Sampling points are located where hazardous gases are used. Throughout the cleanrooms are cable trays which contain the clear sampling tubing and related wires. Throughout the cleanrooms, there are light/horn trees which relate to this system. Below the trees are red emergency gas off (EGO) buttons. They will shut down all gas zones that are related to that area, i.e. EGO in Tylan area will shut off zone 13 only. The monitoring units are in MRC Cleanroom 107 and 240 entrances. The CM4 modules, or monitoring unit, can sample four sites of the same chemical class, but can’t differentiate between gases of that class. For example, a hydride unit can not differentiate between arsine, phosphine or silane. When choosing a sampling set point, the monitor will be calibrated to respond to the gas of greatest hazard.
Located in MRC 240 is the main computer for this system. The computer display located in the lobby is for monitoring only. Anybody can access the graphic overview of alarm & events displayed on the monitor. In the graphic overview, click on desired floor. Monitored areas in the facility are now displayed. One can now click on one of the areas, which will display the lamp tree and monitoring in that area. One can now select a specific sensor by clicking on it. A real time graph will appear for what is being sensed. The alarm & events page can provide a history of events or if it is in summary mode, the last event. When a new alarm event happens, a message will pop up on the screen. This system is designed to shutdown gas flows if unsafe levels are detected; however, plc power failure, exhaust failure, fire detection, or excess pressure on the low pressure side of the gas cylinder manifold will also shut off gas flow. All NNF users will be given instructions to learn the basics of the hazardous gas monitoring system and they will learn how to read/interpret the alarm messages on the computer terminals located on first and second floors.
The gas monitoring system is tied into the building fire alarm system which would only activate if there is a hazardous gas event in the breathing zones.
Gas Cabinets
The gas cabinets are manufactured by Spectra Gases and contain up to two process gases with an independent nitrogen purge system for both purity and safety considerations. All gas cabinets have self-closing / latching doors and a water sprinkler. Each cabinet is vented so that there is a minimum of 200 fpm across the cabinet window when it is open. Anytime the gas monitoring system shuts down a zone, each cabinet in the zone must be inspected before the gas monitoring system is reset. Each gas manifold has a Span gauge on the low pressure side. This gauge has been set for the excess pressure function of the gas monitoring system. They have been calibrated based on the gas that is to be located there; therefore a change in delivery pressure may require a change in Span gauge set points. Only NNF authorized personnel and certified users have access to the gas cabinet zones in the facility. Any change in pressure regulator set points can only performed by NNF personnel.
Cylinder changes may only be performed by trained and authorized personnel. Access to the gas storage rooms is limited to the authorized personnel only.
The high purity gas lines for the corrosive, toxic and pyrophoric gases have a concentric, coaxial structure and have been helically welded to form one continuous piece from the cabinet to the equipment. The process gas flows through the central core and the outer sheath is purged with nitrogen back to the gas cabinet. The outer jacket pressure gauge has both an audible and visual output at the process tool to indicate a drop in pressure.
No process toxic gas piping may be installed or modified without prior approval.
Secondary Air Handler Recirculator
Different sections in the laboratory are supplied by recirculating air units located above the ceiling and in the chase areas. In the case of a fire or chemical spill these units should be deactivated by cutting off the re-circulation fans using knife handle breaker switches located at the entrance of the laboratory and in Room 211, which houses the GCA Autostep 200.
General Equipment Safety
Certain pieces of equipment in the facility are equiped with Emergency Power Off (EPO) Buttons. These buttons can be pressed to immediately remove all power from the tool. In an emergency any user can hit the EPO button to cut off the power, even if not certified on the tool.